The best way to manufacture a moulded rubber or silicone part is by injection moulding. The mould is closed during the injection which saves deflashing times.
Since rubber is a bad at transfer the heat from the warm mould plate, you can shorten the time with injection moulding. This is because you press the rubber or silicone through a nozzle and also through a canal system, then you get a pressure drop in the detail. The pressure energy changes to heat energy, which means that the rubber paste is preheated. This allows the vulcanisation time to be reduced compared to compression.
The machine is fed with a rubber strap and draws new material when the screw starts. This also means that it is not necessary to produce preformed rubber substances before the pressing operation.
Curing temperature is between 150ºC – 200ºC. Cycle time varies depending of amount of rubber and the thickness of the rubber detail.
Automation is possible.
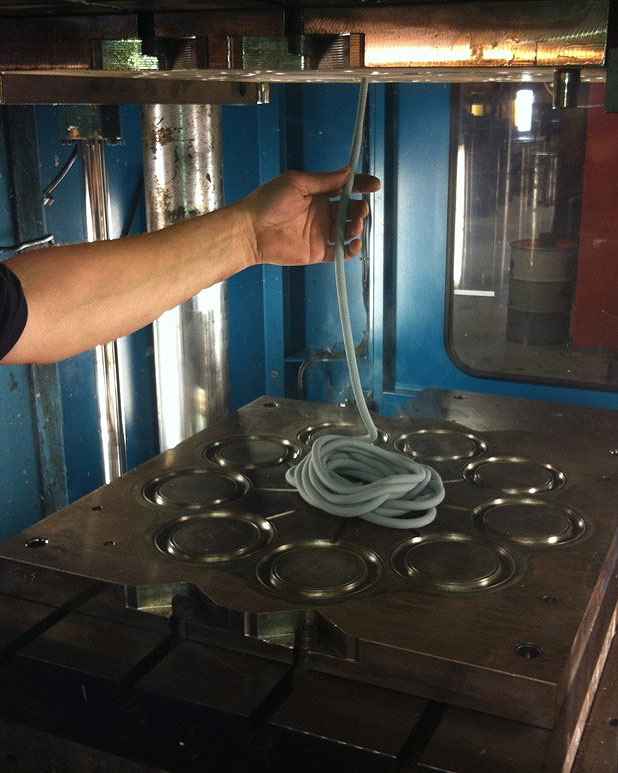